PWM v Air Induction for Drift Management & Coverage
Pulse Width Modulated (PWM) equipped boom sprayers have been gaining popularity in Australia over the last few years, the most visible new players being Agrifac with their SSP (Strict Spray Plus) system and more recently John Deere’s ExactApply. Before both of those of course, Case’s Patriot.
Just quickly on how PWM differs from pressure regulated sprayers.
With a pressure regulated sprayer using Air Induction Nozzles, the rate per hectare is maintained by the spray controller adjusting the pressure to compensate for changes in speed.
With PWM, the nozzles are ‘pulsing’ on and off for a certain amount of times per second. If the system pulses 10 times or 15 times or 30 times, that’s the Hertz rating for that system. The way that speed variations are compensated for to maintain a constant rate per hectare is to vary the percentage of time within each pulse or cycle that the nozzle is actually on or open. That percentage is called the Duty Cycle and is how the pressure is maintained as a constant.
There has been a focus on the benefits that PWM has to offer over conventional pressure regulated sprayers which mainly use Air Induction nozzles as the primary means of drift reduction. That is not to ignore the other important factors for minimizing drift like operating speeds, boom height and weather, just we’re focusing here on nozzles.
Basic advantages afforded by PWM
- Constant pressure setting allows selection and maintenance of a specific Spray Quality.
- Broad range of operating speeds within Duty Cycle limitations.
- Enables turn compensation again within Duty Cycle limitations.
Note that multi-tiered systems can generally handle the maintenance of Spray Quality, it's the introduction of new advanced quad nozzle systems into the market recently, that all of these benefits above are no longer unique to PWM although price-wise, I think PWM may have the edge.
Now consider this, generally as a nozzle gets bigger, its Spray Quality increases. Yes?
Also consider that non-air induction nozzles are generally required to be used with PWM systems.
On a size for size comparison between Air Induction and NON Air Induction nozzles, the Air Induction nozzle will usually (according to its manufacturers' specifications) demonstrate superior drift reduction, but we are not looking at a size for size comparison as we shall see.
The way the PWM systems work, given that the nozzle may be off for anywhere up to 40% or so of the time, it requires a much bigger nozzle than the conventional sprayer using Air Induction nozzles to crank out the dose required while it is on.
Again generally speaking, bigger nozzle, increased Spray Quality, more drift reduction. As to which offers ’the best’ drift reduction, that would be very difficult to say with precision. What I will say is that each nozzle type offers excellent choices in drift reduction to suit the specific system.
Spray Quality V Droplet Size (important distinction)
It is a common claim that PWM enables you to select a specific droplet size. To pick that nit, I prefer to use the term Spray Quality because the nozzles produce a wide range of droplets and the Spray Quality rating represents the mean or average droplet size within all of that mix (at a particular pressure). More importantly, the term Spray Quality has legal weight on your product label.
With the pressure regulated sprayer, the pressure changes required to maintaining the constant rate per hectare may cause the nozzle to transition from one Spray Quality to another. This is not necessarily a bad thing in terms of efficacy and can even be a desirable characteristic however, it can be a problem if an unplanned change in Spray Quality results in non-compliance with your product label. Obviously, 2,4-D falls into that category.
Either way, it is important for operators to be aware of the transition pressure between Spray Qualities for the nozzles they are using. This basic information will be found on every nozzle chart, including the main reference charts for both Air induction and PWM nozzles published below by the GRDC.
At nozzles.online we offer more detailed transition pressures than the usual chart which look like this. Here is what the basic and our more detailed Spray Quality transition charts look like, for our standard PWM 2,4-D nozzle, the Twin Fan Low Drift:
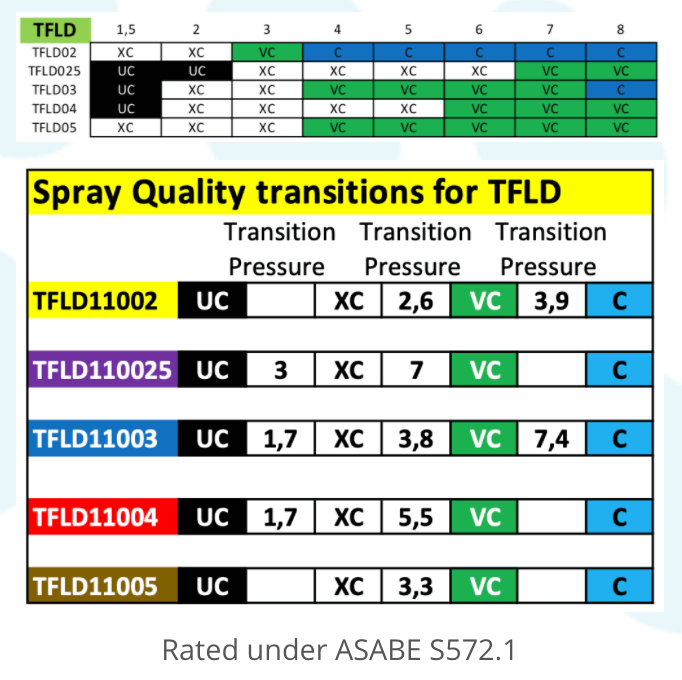
To wrap up, on whether or not PWM or AI is the absolute best for drift management, the absolutely precise answer to the question is…. It depends, just pick from the options available for your sprayer type. There is plenty of information about, and people like me you can call for help if you need it.
Following added on Saturday June 27, 2020
So what about coverage then?
When I posted this article on Twitter, it sparked a conversation that morphed into discussion about “coverage” as a result of PWM machines typically requiring larger nozzles. (not necessarily the case for PWM sprayers on closer spacings or using pairs of nozzles requiring downsizing nozzles)
There was speculation that Air Induction nozzles, when compared with non-air induction PWM nozzles, may provide a better result coverage-wise.
That discussion was resolved by Tom Wolf (@nozzle_guy) who contributed this to the conversation.
"If same spray quality and same water volume, then same coverage, even with PWM. As Dave said, the brief shut off essentially disappears due to: 1. 180-degree timing offset to adjacent nozzles; 2. Blending of spray cloud en route to canopy from boom height and travel speed."
One coverage issue that comes up occasionally is the potential for "skip", caused by a set of circumstances interrupting the blending process. According to the Bill's (Gordon and Campbell), that may occur with a combination of low Hz, low boom, and/or low Duty Cycle. Link to publication.
As to duty cycle, the GRDC Fact Sheet recommends a higher duty cycle generally, which has to do with 10 Hz machines representing the largest population. The recommendations for a lower Duty Cycle of around 70% to facilitate turn compensation come along with higher Hz hardware now on the market.
What about reasons for even choosing PWM in the first place?
Soon after the coverage matter was resolved, Peter Newman (@peterdnewman) inquired;
"Are there benefits of PWM in large open paddocks with straight runs. I get the PWM is great for turn compensation, but is it necessary to go to the expense / complexity in straight, open paddocks?"
I didn’t need Tom's help on this one; the answer has been given to me by my own customers and apart from the obvious (turn compensation) that is simply integration (or to be ready for integration) with cameras for optical weed spraying. An example below from the GRDC's publication on PWM in 2019.
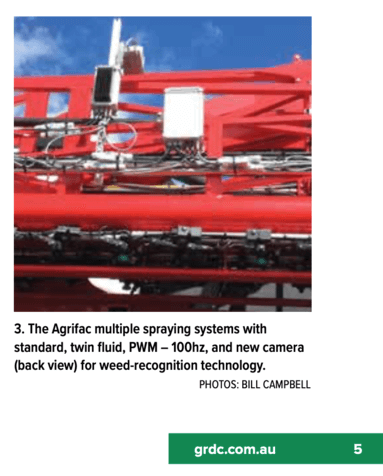
So overall, PWM systems are well and truly established in today's market and it would appear that properly set up, they are a good each-way bet on performance for both drift management and coverage compared with Air Induction.
Regards,
Dave Young
08 6102 5886
PS… note that if you find your way to the GRDC charts, you will find many ARAG nozzle options for your boom sprayer in both the Air Induction and PWM sections.
GRDC Nozzle Selection Guide